Much has been written regarding the significance of the
notched bar impact testing of steels and other metallic
materials. The Charpy and Izod type test relate notch
behavior (brittleness versus ductility) by applying a single
overload of stress. The results of these tests provide
quantitive comparisons but are not convertible to energy
values useful for engineering design calculations. The
results of an individual test are related to that particular
specimen size, notch geometry and testing conditions
and cannot be generalized to other sizes of specimens
and conditions.
The results of these tests are useful in determining
the susceptibility of a material to brittle behavior when
the applied stress is perpendicular to the major stress.
In externally threaded fasteners, however, the loading
usually is applied in a longitudinal direction. The impact
test, therefore, which should be applicable would be one
where the applied impact stress supplements the major
stress. Only in shear loading on fasteners is the major
stress in the transverse direction.
Considerable testing has been conducted in an effort
to determine if a relationship exists between the Charpy
V notch properties of a material and the tension properties of an externally threaded fastener manufactured
from the same material.
Some conclusions which can be drawn from the
extensive impact testing are as follows:
1. The tension impact properties of externally threaded
fasteners do not follow the Charpy V notch impact pat-
tern.
2. Some of the variables which effect the tension impact
properties are:
A. The number of exposed threads
B. The length of the fastener
C. The relationship of the fastener shank diameter to
the thread area.
D. The hardness or fastener ultimate tensile strength
Following are charts showing tension impact versus
Charpy impact properties, the effect of strength and
diameter on tension impact properties and the effect of
test temperature.
Please note from figure 21 that while the Charpy
impact strength of socket head cap screw materials are
decreasing at sub-zero temperatures, the tension impact
strength of the same screws is increasing. This compares
favorable with the effect of cryogenic temperatures on
the tensile strength of the screws. Note the similar
increase in tensile strength shown in figure 22.
It is recommended, therefore, that less importance be
attached to Charpy impact properties of materials which
are intended to be given to impact properties for threaded
fasteners. If any consideration is to be given to impact
properties of bolts or screws, it is advisable to investigate
the tension impact properties of full size fasteners since
this more closely approximates the actual application.
Fastener Material
For Concentration-Cell Corrosion: Keep surfaces
smooth and minimize or eliminate lap joints, crevices,
and seams. Surfaces should be clean and free of organic
material and dirt. Air trapped under a speck of dirt on the
surface of the metal may form an oxygen concentration
cell and start pitting.
For maximum protection, bolts and nuts should have
smooth surfaces, especially in the seating areas. Flushhead bolts should be used where possible. Further,
joints can be sealed with paint or other sealant material.
For Fretting Corrosion: Apply a lubricant (usually oil)
to mating surfaces. Where fretting corrosion is likely to
occur: 1. Specify materials of maximum practicable hardness. 2. Use fasteners that have residual compressive
stresses on the surfaces that may be under attack. 3.
Specify maximum preload in the joint. A higher clamping
force results in a more rigid joint with less relative move-
ment possible between mating services.
For Stress Corrosion: Choose a fastener material that
resists stress corrosion in the service environment.
Reduce fastener hardness (if reduced strength can be
tolerated), since this seems to be a factor in stress
corrosion.
Minimize crevices and stress risers in the bolted joint
and compensate for thermal stresses. Residual stresses
resulting from sudden changes in temperature accelerate
stress corrosion.
If possible, induce residual compressive stresses into
the surface of the fastener by shot-peening or pressure
rolling.
For Corrosion Fatigue: In general, design the joint
for high fatigue life, since the principal effect of this form
of corrosion is reduced fatigue performance. Factors
extending fatigue performance are: 1. Application and
maintenance of a high preload. 2. Proper alignment to
avoid bending stresses.
If the environment is severe, periodic inspection is
recommended so that partial failures may be detected
before the structure is endangered.
As with stress and fretting corrosion, compressive
stresses induced on the fastener surfaces by thread
rolling, fillet rolling, or shot peening will reduce corrosion
fatigue. Further protection is provided by surface coating.
TYPES OF CORROSION
Direct Attack°most common form of corrosion affecting
all metals and structural forms. It is a direct and general
chemical reaction of the metal with a corrosive mediumliquid, gas, or even a solid.
Galvanic Corrosion°occurs with dissimilar metals contact.
Presence of an electrolyte, which may be nothing more
than an individual atmosphere, causes corrosive action
in the galvanic couple. The anodic, or less noble material,
is the sacrificial element. Hence, in a joint of stainless
steel and titanium, the stainless steel corrodes. One of
the worst galvanic joints would consist of magnesium
and titanium in contact.
Concentration Cell Corrosion°takes place with metals in
close proximity and, unlike galvanic corrosion, does not
require dissimilar metals. When two or more areas on
the surface of a metal are exposed to different concentrations of the same solution, a difference in electrical
potential results, and corrosion takes place.
If the solution consists of salts of the metal itself, a metal-
ion cell is formed, and corrosion takes place on the sur-
faces in close contact. The corrosive solution between
the two surfaces is relatively more stagnant (and thus
has a higher concentration of metal ions in solution) than
the corrosive solution immediately outside the crevice.
A variation of the concentration cell is the oxygen cell in
which a corrosive medium, such as moist air, contains
different amounts of dissolved oxygen at different points.
Accelerated corrosion takes place between hidden
surfaces (either under the bolt head or nut, or between
bolted materials) and is likely to advance without
detection.
Fretting°corrosive attack or deterioration occurring
between containing, highly-loaded metal surfaces sub-
jected to very slight (vibratory) motion. Although the
mechanism is not completely understood, it is probably
a highly accelerated form of oxidation under heat and
stress. In threaded joints, fretting can occur between
mating threads, at the bearing surfaces under the head
of the screw, or under the nut. It is most likely to occur in
high tensile, high-frequency, dynamic-load applications.
There need be no special environment to induce this
form of corrosion...merely the presence of air plus vibra-
tory rubbing. It can even occur when only one of the
materials in contact is metal.
Stress Corrosion Cracking°occurs over a period of time
in high-stressed, high-strength joints. Although not fully
understood, stress corrosion cracking is believed to be
caused by the combined and mutually accelerating
effects of static tensile stress and corrosive environment.
Initial pitting somehow tales place which, in turn, further
increases stress build-up. The effect is cumulative and, in
a highly stressed joint, can result in sudden failure.
Corrosion Fatigue°accelerated fatigue failure occurring
in the presence of a corrosive medium. It differs from
stress corrosion cracking in that dynamic alternating
stress, rather than static tensile stress, is the contributing
agent.
Corrosion fatigue affects the normal endurance limit of
the bolt. The conventional fatigue curve of a normal bolt
joint levels off at its endurance limit, or maximum
dynamic load that can be sustained indefinitely without
fatigue failure. Under conditions of corrosion fatigue,
however, the curve does not level off but continues
downward to a point of failure at a finite number of
stress cycles.
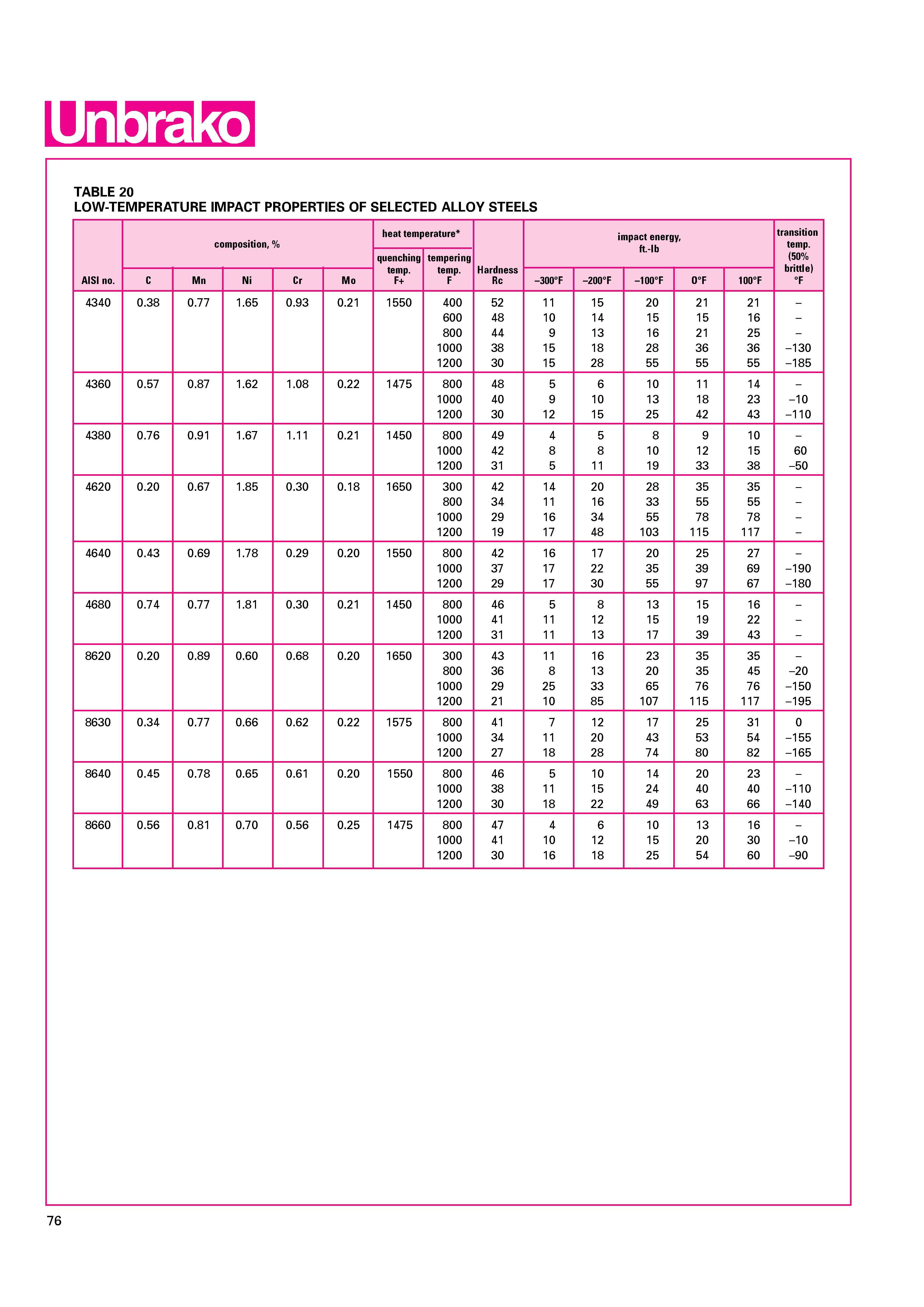
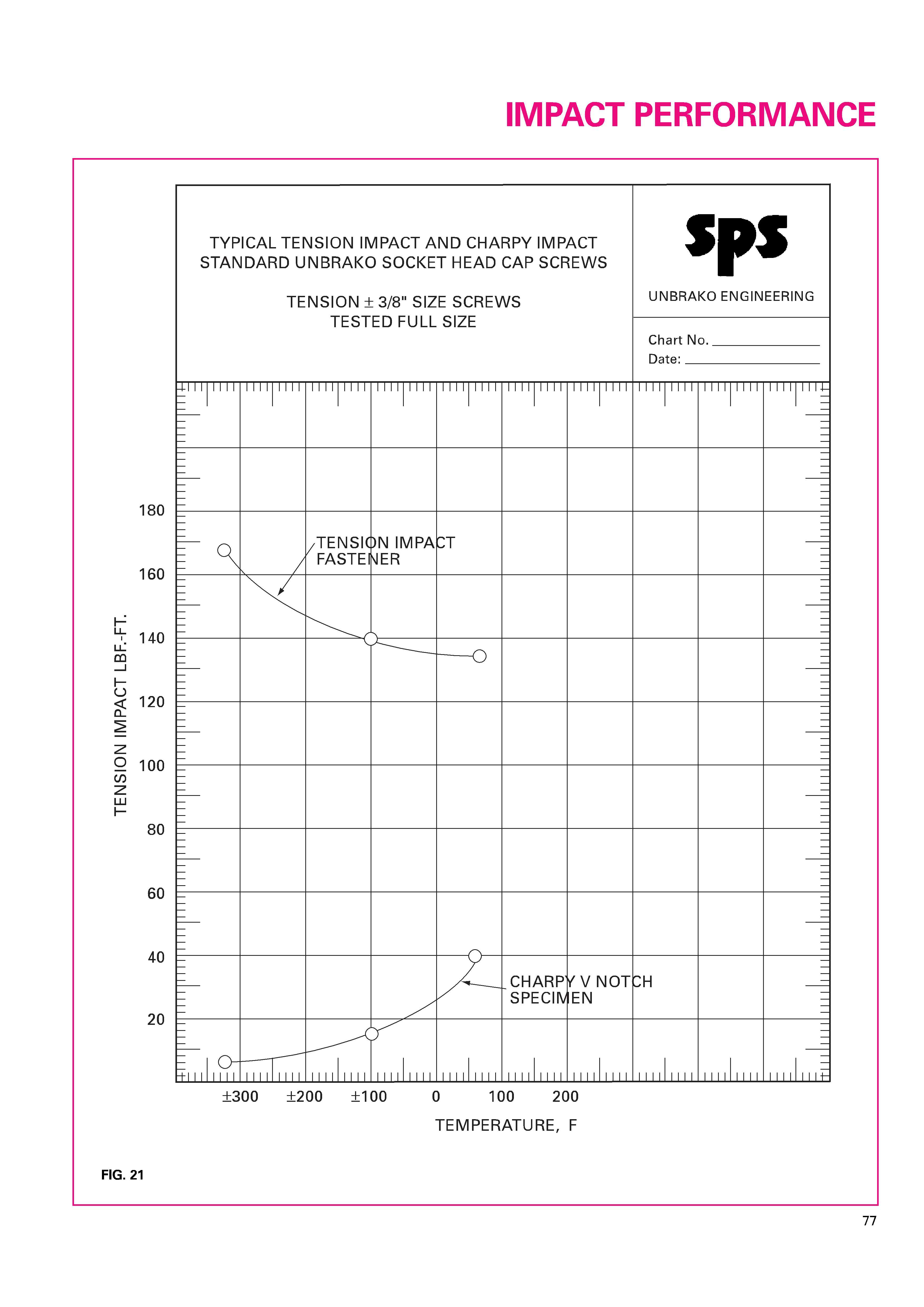
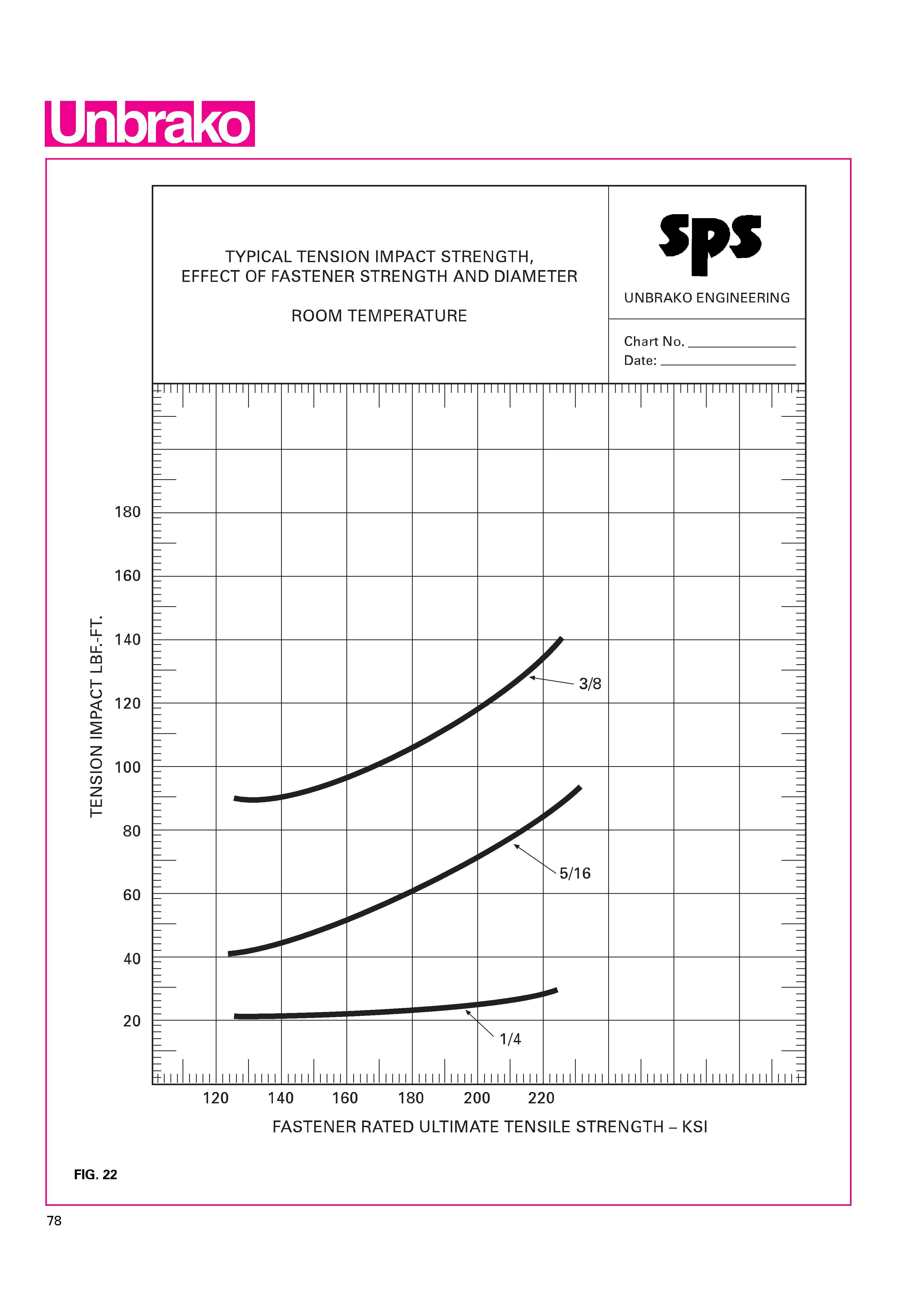